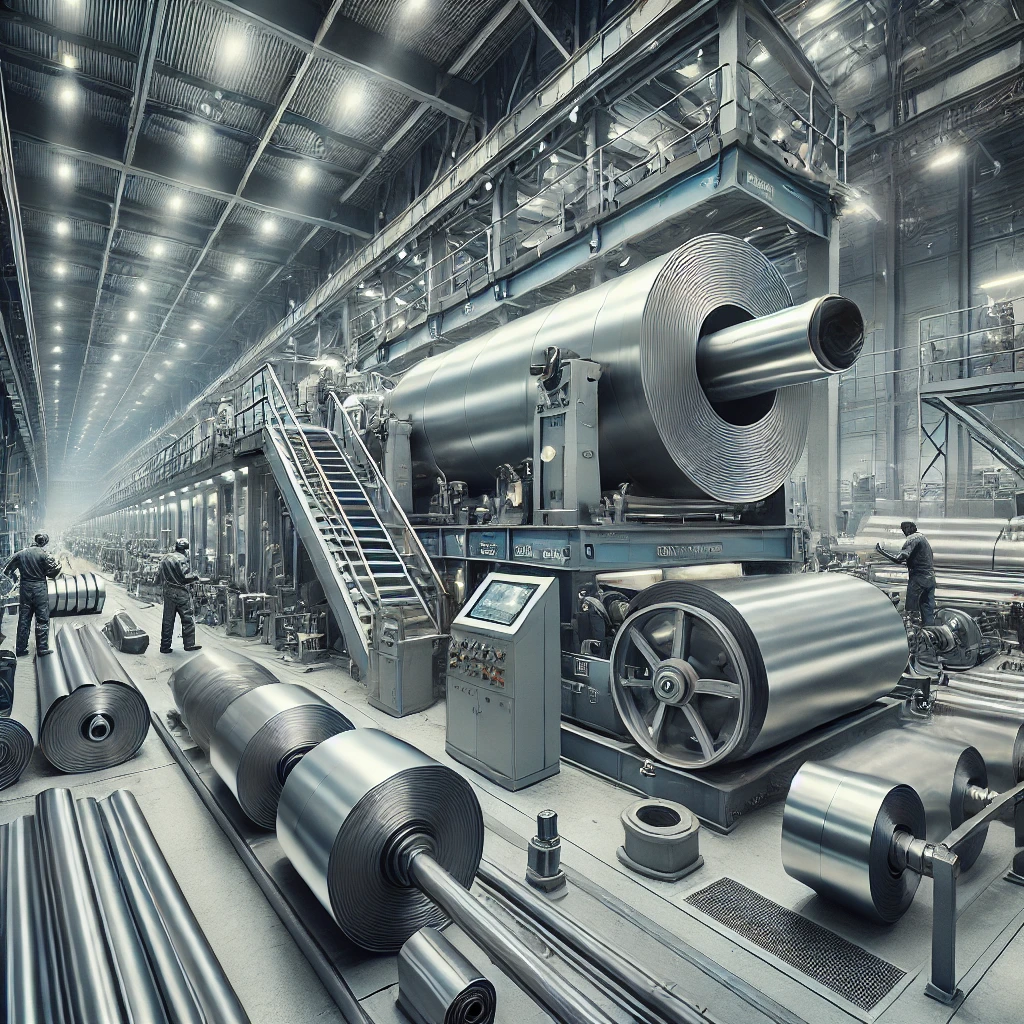
In the world of HVAC systems, ductwork plays a crucial role in ensuring efficient air distribution throughout a building. One of the most common and effective types of ductwork is rolled ductwork. This blog will delve into the intricate process of rolled ductwork manufacturing, highlighting its importance, benefits, and the precision involved in creating these essential components.
What is Rolled Ductwork?
Rolled ductwork refers to ducts made from metal sheets that are rolled into a cylindrical or spiral shape. These ducts are essential for air distribution systems in residential, commercial, and industrial buildings. The rolling process allows for a strong, durable, and flexible duct that can handle various pressures and air volumes.
The Manufacturing Process
- Material Selection:
- The process begins with selecting the appropriate metal. Common materials include galvanized steel, stainless steel, and aluminum. The choice of material depends on the application, budget, and specific requirements of the project.
- Sheet Metal Cutting:
- Large metal sheets are cut to size using precise cutting equipment. The dimensions are based on the ductwork design, ensuring that the sheets are ready for the rolling process.
- Rolling the Metal:
- The cut metal sheets are fed into a rolling machine. This machine gradually shapes the flat sheet into a cylindrical or spiral form. The rolling process must be carefully controlled to maintain uniformity and prevent any deformities in the duct.
- Seaming and Welding:
- Once rolled, the edges of the metal sheets are joined together. This can be done using various methods such as lock forming, welding, or using a seam closure. The seam must be airtight to ensure no air leakage during operation.
- Flanging and Beading:
- The ends of the ducts are flanged or beaded to allow easy connection to other duct sections or HVAC components. This step is crucial for ensuring a secure and efficient assembly.
- Quality Control:
- Each duct is inspected for quality and precision. This includes checking the dimensions, seam integrity, and overall finish. Any defects must be addressed before the ducts can be dispatched.
- Coating and Insulation (Optional):
- Depending on the application, the ducts may be coated with protective layers or insulated to improve energy efficiency and reduce noise.
Benefits of Rolled Ductwork
- Durability: Rolled ductwork is known for its strength and durability, making it suitable for various environments.
- Efficiency: The smooth, cylindrical shape reduces air resistance, ensuring efficient airflow.
- Flexibility: Rolled ducts can be custom-made to fit specific design requirements, providing flexibility in HVAC system design.
- Airtight Seams: Properly seamed ducts minimize air leakage, improving overall system efficiency and performance.
Applications of Rolled Ductwork
Rolled ductwork is used in a wide range of applications, including:
- Residential HVAC Systems: Ensuring comfortable and efficient air distribution in homes.
- Commercial Buildings: Providing large-scale air distribution for offices, malls, and other commercial spaces.
- Industrial Facilities: Handling the high air volume and pressure requirements in factories and warehouses.
Innovations in Rolled Ductwork Manufacturing
The field of ductwork manufacturing is continuously evolving with advancements in technology. Modern rolling machines offer higher precision and automation, reducing the time and labor required. Additionally, new materials and coatings are being developed to enhance the performance and longevity of rolled ductwork.
Conclusion
Rolled ductwork manufacturing is a critical aspect of the HVAC industry, ensuring efficient and reliable air distribution in various settings. The process requires precision, expertise, and a commitment to quality. As technology advances, we can expect even more innovations in this essential field, contributing to better HVAC systems and improved indoor air quality.
For more information on rolled ductwork manufacturing and other HVAC solutions, visit www.heavymetalfabrication.com.